Conveyors and palletizers are key components in an effort by dairy processors to enhance production efficiencies.
With the technologies becoming increasingly robust and sophisticated, operators can increase output, minimize expenses, and enhance food and worker safety by leveraging the optimal designs. Yet, with a plethora of options to consider, pinpointing the most effect equipment can be vexing.
“Dairy processors’ greatest challenge is selecting the right conveyor system for their specific application,” says Lindsey Muchka, director of marketing at Dorner Manufacturing Corp., a Hartland, Wis.-based conveyor developer.
Processors, however, often view conveyors as the last items to plan and purchase, despite the equipment being vital for supporting throughput rates, says Ken Lento, SBU manager, Central & Optical and West, for FlexLink Systems Inc., an Allentown, Pa.-based conveyor and palletizer provider.
Conveyors also can increase overall equipment effectiveness and uptime by reducing sanitation cycle times and costs, says Brian Bancroft, applications group manager for Nercon Engineering and Manufacturing Inc., a Neenah, Wis.-based developer of conveyor systems.
The importance of properly sanitizing equipment requires processors to understand the hygienic requirements when selecting technologies, he states. Bancroft notes, for instance, that because unwrapped, ready-to-eat products require the highest level of sanitary design, operators should leverage systems with minimal harborage points, the appropriate metal finishes, and removable wear strips and guide rails for easy cleaning.
It is essential too that processors understand the difference between sanitary and stainless-steel conveyors, Muchka adds. “Just because a conveyor is stainless-steel doesn’t necessarily mean it’s sanitary,” she says.
While stainless-steel conveyors can withstand regular washings with light chemical cleaning agents, a true sanitary platform does not contain the catch areas that can enable water, particulates, and bacteria to accumulate in the food zone, Muchka states.
Automation is the answer
An innovative conveyor system also incorporates sensors that enable operators to receive processing and product data in real time and automatically precipitate adjustments to other equipment on the line, says Rudy Sanchez, food handling systems product manager at Key Technology, a Walla Walla, Wash.-based conveyor system developer.
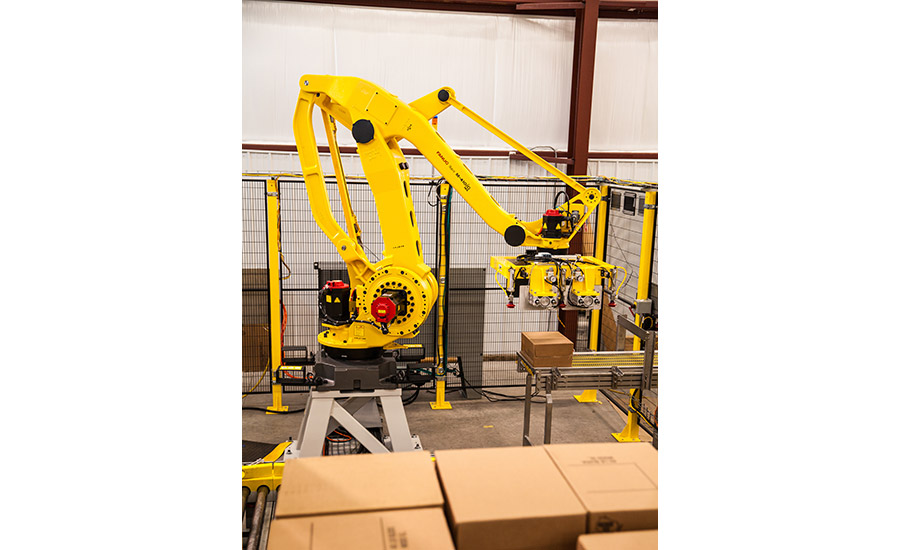
After recording a product’s weight, for instance, sensors can trigger the opening of an upstream gate on a vibratory conveyor to feed the optimal amount of product to maximize output, he notes. In addition, a metal detector can activate a dump gate to discard the section of product that contains metal pieces, Sanchez says.
“Highly functional conveyor systems allow for fast, reliable, and flexible handling of various case sizes, SKUs, and pallet configurations,” says Tom Luft, sales and application manager for NCC Automated Systems, a Souderton, Pa.-based conveyor supplier. “When systems are designed and installed properly, output is increased and the number of operators can be significantly decreased.”
Automated palletizers can boost efficiencies as well by operating non-stop and replacing a workforce that is subject to body strains from repetitive bending and lifting, says Megan Pickett, business development leader for Zepnick Solutions Inc., a Green Bay, Wis.-based provider of palletizing systems. “This strenuous physical effort often leads to work-related injuries for valuable employees, which causes production delays and stoppages,” she notes.
Robotic palletizers also can consistently stack pallets in the same pattern while enabling operators to easily change patterns with a push of a button or by easily accessing a dashboard or screen, Pickett states. Nevertheless, it can be difficult for processors to financially justify robotic palletizing if they are only running one shift of production, says Dan Altman, vice president of sales and marketing for Delkor Systems Inc., a St. Paul, Minn.-based palletizer developer.
“However, if there are more than one person, more than one shift, and workers have had costly injuries, justification increases dramatically,” he states.
A plethora of possibilities
In deciding on the optimal conveyor and palletizing systems to install, processors should consider such factors as floor space, the number of SKUs to manage, case rates and weights, and pallet patterns, Lento says.
“Building a system with input from all departments, including maintenance, engineering, sanitation, quality assurance, safety, and production, also is critical for meeting plant KPIs [key performance indicators] and reducing the total cost of ownership,” says Andrew Roloff, dairy account manager for Intralox LLC USA, a New Orleans-based conveyor system developer. “Production efficiencies and throughput numbers are reliant on having functional systems, but QA [quality assurance] and sanitation workers also need a conveyor system that reduce the risks of product contamination.”
Additional considerations include the type of belting to incorporate, which can vary by the dairy product under development; the chemicals that will have contact with equipment; and if systems will undergo clean-in-place or clean-out-of-place sanitizing, he notes.
It is critical for management to assess the necessary production capacity and processing speed for both current and future demands as well, notes Hannah Maes, head of marketing for Frain Industries, a Carol Stream, Ill.-based supplier of conveyors and palletizers. “Consider the range of dairy products to be handled as different products may require specific conveyor and palletizer configurations,” she says, noting that systems must have the flexibility to support products in a wide array of shapes and sizes without damaging the goods.
Processors also should ensure that designs can integrate with existing automation and control systems and learn if suppliers can customize equipment to meet specific processing requirements and facility constraints, Maes notes.
Further palletizer selection criteria include the number of items per minute that the technologies can support; the amount of SKU sizes, weights, and shapes a system will need to manage; and overall system integration, Pickett says. Among the integration variables are how products will reach the palletizer; if finished pallets will utilize stretch wrap; and ways a palletizer will impact workflow, she notes.
Operators must settle on palletizer type as well, such as whether to incorporate robotic, conventional, hybrid, automatic, semi-automatic, or high or low equipment, says Bryan Sinicrope, vice president of marketing and integrator sales for A-B-C Packaging Machine Corp., a Tarpon Springs, Fla.-based palletizer supplier.
“The right machine will depend on many factors, which is why it is important to evaluate requirements and goals and share those with the prospective suppliers who can help guide decisions,” he notes.
Processors should also work with integration experts who have experience delivering complete systems and allocate adequate amounts of the capital expenditure budget to training, maintenance, and future equipment enhancements, Luft states. He adds, however, that “no system is perfect and it will need to be refined over time to maximize effectiveness and efficiency.”
Rate the return
It is crucial too that processors look beyond the purchase price when evaluating technology options, Sinicrope says.
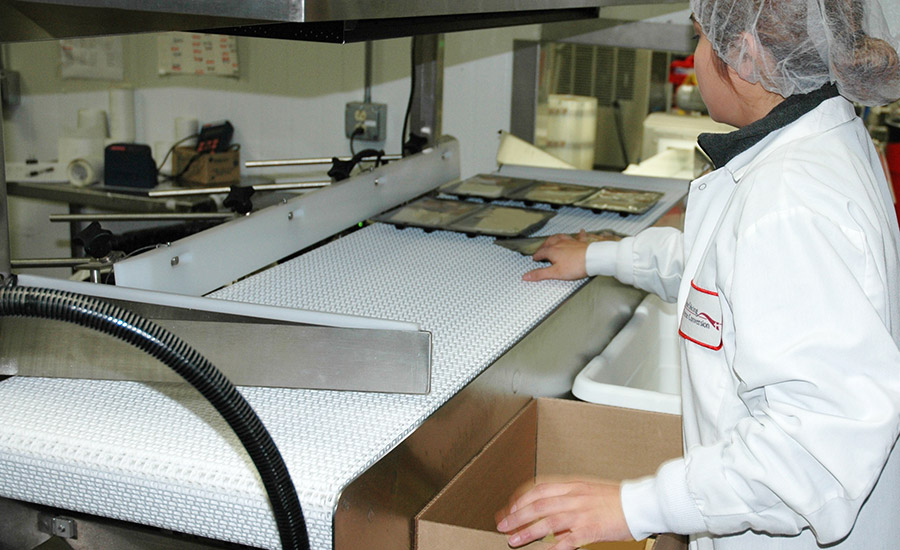
“It may be appealing to seek the least-cost solution and a quick payback,” he states. “However, this can be shortsighted. Factor in the costs of installation, operation, training, maintenance, changeover, upgrades, spare parts, and even utilities, as these costs will impact the ultimate return on investment.”
Calculating the return on investment (ROI) also involves analyzing the savings from replacing workers with technologies, Lento says. “Companies may also worry about capital investment and being able to sustain more complex equipment,” he states. “But if done right, automation can run with minimal downtime and in a sustainable way.”
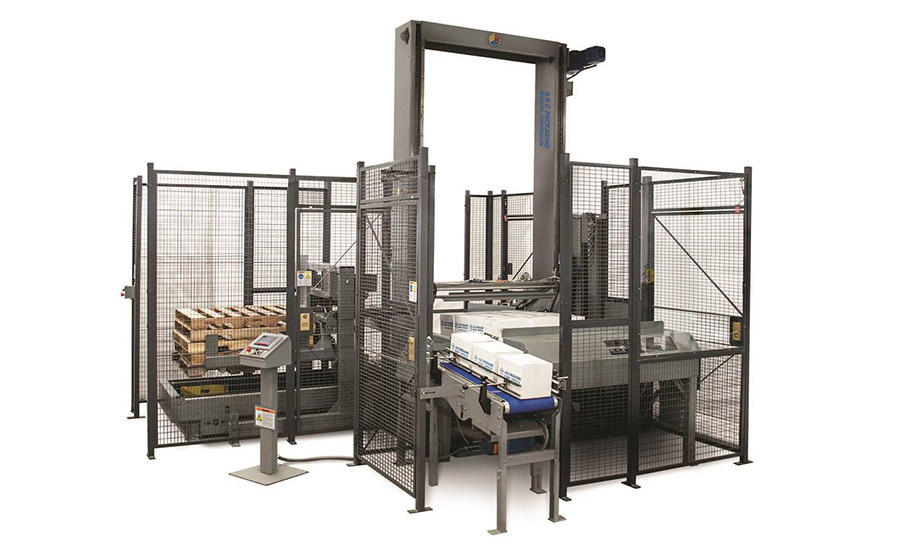
Concerns about operating expenses and worker ergonomics are among the top reasons many operators choose robotic palletizing, Altman says. “If you can eliminate labor, and reduce repetitive motion injuries, you will save money on all fronts,” he states. “In addition, many dairies may require palletizing in cooler areas. This means it is extremely hard to not only retain employees, but to find them in the first place.”
Indeed, hiring workers for manual labor positions, including those who are willing to work the second or third shift and show up reliably and on time every day, is becoming increasingly difficult, says Jim Mallory, Frain Industries engineering lead. That makes using robotic palletizers, which can minimize damage-creating errors and help eliminate worker compensation claims, particularly attractive, he notes.
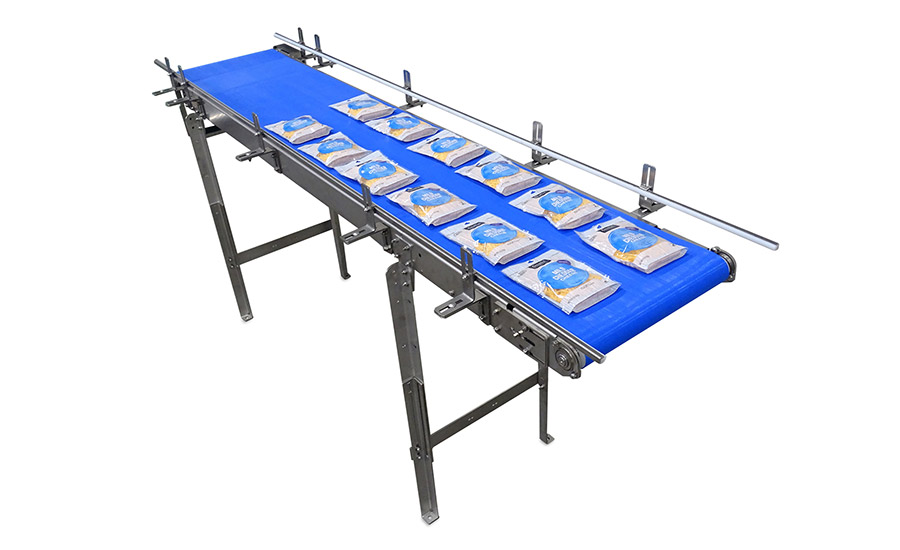
“More companies also are minimizing their risk and cost by renting machinery,” Mallory states. “This shortens the companies’ approval process as rentals are typically categorized as an operating expense, which most companies have available.”
A bright forecast
Conveyors and palletizers are set to become even more effective as developers engineer designs that support faster processing rates, a greater assortment of product sizes, and newer styles of packaging materials, Luft says.
“Conveyors will continue to evolve in ways that simplify sanitation requirements and reduce the cost of ownership,” Sanchez adds, which includes more smart automation and artificial intelligence features to enhance line efficiency and reduce the need for operator intervention.
Automated equipment that enhances worker safety by slowing or shutting down when employees get too close to the units will become more prevalent as well, particularly for facilities with limited workspace, Altman says. “The days of huge footprints with safety fencing will diminish as floorspace has gotten too important,” he notes.
More suppliers, meanwhile, are designing conveyors in accordance with the unique specifications of a processor’s production line, which includes meeting speed and sanitation requirements, Muchka says.
“Often, applications call for products to be positioned in a specific way, in an exact location on a conveyor, and be ready for the next step in the process,” she says. “These are rapid-fire actions, and the conveyor needs to perform as expected to meet the applications’ demands.”
Processors, however, should not settle for a conveyor that is shoe-horned into an application, especially when developers can engineer a system that seamlessly integrates into a larger process, Muchka concludes, adding “to do that requires an understanding of what the goals and expectations are for the conveyors.