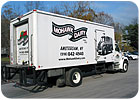
Mohawk drivers say an integrated lift platform system from Johnson Truck Bodies makes deliveries faster, safer, and more rewarding.
Mohawk Dairy, Amsterdam, N.Y., takes equal care with its route drivers as it does with its products and customers. That's evidenced in that when it recently updated its fleet to larger truck bodies, it also included the PowerPlatform from Johnson Refrigerated Truck Bodies, Rice Lake, Wis.
In 1932, with skills learned in the old country, Zygmunt Rzeszotarski founded Mohawk Dairy in Amsterdam, a small town near Albany. Back then it was just Zygmunt, a small processing plant the size of a modest home, and a single truck.
Today, Zygmunt's son and two grandsons manage the business, which has grown to eight trucks serving more than 750 customers. The old-world traditions of processing and distributing fresh dairy haven't been forgotten at Mohawk Dairy, but the technology and method of delivery has changed.
Most deliveries are made through Mohawk's private, refrigerated trucks, owned and operated by the company. Self-delivery ensures the Mohawk name lives up to the fresh quality standards of the Rzeszotarski family. High standards of freshness and quality have helped Rich Rzeszotarski and his two sons grow their business in the past 75 years. They now serve the entire region of New York State.
"We've been using Johnson Refrigerated Truck Bodies for more than 20 years," said Rich Jr., grandson of the founder. "There's nothing like them on the market. Upkeep is minimal, especially on our newer trucks with Johnson's stainless steel floors and new, improved stainless steel hardware on the outer body of the truck. The cold plates are reliable, and the bodies look as good as new for years. We probably would still have the original trucks purchased 20 years ago, but as our business grew we traded up from 18-foot bodies to 22-foot bodies."
New technology replaces old-style lift gates
In addition to trading smaller bodies for larger ones, the Rzeszotarski's, found a way to provide drivers with more safety and satisfaction. In 2004 Rich Jr. saw a demo of Johnson's trade-marked PowerPlatform, and immediately ordered two for existing trucks. They now have three Johnson power lifts."Before Johnson, the fold out lift gates and old-fashioned ramps we used were cumbersome," said Rich Jr. "The driver had to back the truck up to the delivery area, unfold the gate, go back in the truck and move forward to adjust the gate, and then readjust the gate. Our drivers make approximately 30 stops a day-so the time saved really adds up. Our drivers say they like the new power lift because it makes their job easier and safer."
PowerPlatform is an in-body drop floor system that can hold up to 3,000 pounds of refrigerated product. Ideal for Direct Store Delivery, the lift quickly lowers driver and product to street level. Because the PowerPlatform eliminates the traditional lift gate at each delivery stop, driver productivity increases and fatigue and worker compensation claims decrease.
"Johnson's power lift saves time and prevents driver fatigue," said Rich Jr. "Drivers say that the new power lift saves at least five minutes per stop. Multiply that by the 35 stops they do each day, and the time savings really add up. The cost of a high-quality lift is insignificant when compared with a driver's back injury."
Johnson Refrigerated Truck Bodies is an innovator and manufacturer of molded fiberglass refrigerated truck bodies and specialized trailers that range from 6- to 36-ft. in length. In business since 1932, Johnson Refrigerated Truck Bodies is a Carlisle Company.
To find out more about Johnson's products visit www.johnsontruckbodies.com.