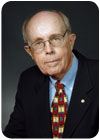
Warehouse Management Systems (WMS) range in combinations of scope, scale, technology and hardware usage from simple software programs tracking inventory, receiving, shipping and pallet putaway to complex automated storage and retrieval systems (AS/RS). They may be stand-alone or operating components of a larger manufacturing system or an even larger business enterprise management system. The incorporation of a WMS as an integral component of the larger business enterprise is, in most instances, a recent event.

In today's world, a WMS can be just about anything you want it to be or can imagine. There also lies the root cause of many of the problems that arise after warehouse management systems are put into service. Warehouse management systems can be designed and utilized to incorporate simultaneous accomplishment of multiple objectives beyond the traditional inventory management functions. In actual practice, a WMS can be designed to solve wide ranging problems, increase productivity, improve accuracy and service quality, reduce costs and inventory, and speed production. The warehouse management system, thus, becomes an integral working part in the overall business operating process as opposed to a free-standing system.
But, possibly the most common mistake made with designing and implementing new warehouse management systems and major modifications is being "penny wise and pound foolish" with the time and money invested in the initial WMS "concept" or "vision" part of the plan. It may be that due to a lack of internal knowledge or adequate external awareness of alternative methods and systems that significant opportunities are missed or overlooked. A relatively small investment in qualified outside third-party technical advice and assistance may bring a host of new choices and opportunities for consideration during the planning process.
All too frequently, failure in the upfront planning to adequately research alternatives, analyze current needs and future plans and to effectively involve all the "stake holders" in the planning dialogue, leads to problems and disappointment (if not disaster) when the finished system goes into service. It's not uncommon to find warehouse or distribution center productivity improvement, cost reduction and capacity expansion projects that were designed and implemented internally by the "warehouse management" staff. Without adequate planning and impact assessment involvement or input from the sales, distribution, accounting and production groups, warehouse gains may have been achieved by transferring warehouse inefficiencies "out the dock door" to distribution, transportation and other areas.