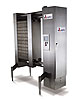
As energy costs continue to drive up the cost of production, dairy processors are looking to squeeze every last ounce of efficiency out of every piece of equipment they own. Heat exchangers have not escaped this scrutiny.
We asked several suppliers of heat exchangers to the dairy industry for their observations and insight on what processors are looking for and how the supplier community can help them in their quest for premium efficiency. Here are their responses:
DFR: What are dairy processors looking for in their heat exchangers? What is the current state of the market (new equipment vs. extending life of existing equipment)?
John Bohn, founder/director of sales and marketing, AGC Heat Transfer Inc.: Many dairy processors using plate heat exchangers are faced with aging, outdated and inefficient equipment. Oftentimes the frames have deteriorated beyond repair and they are faced with the difficult task of maneuvering an old piece of equipment out and a new one in with little or no time or real estate.
Jim LeClair, regional director, product management, APV: Dairy processors are looking to maximize their efficiency of their heat-exchange equipment. The costs of energy and food safety requirements are driving the producers to make sure that the ability to keep their equipment in optimum condition at all times.
Right now, it seems to be a mixed market, with some of the processors revamping their entire heat-exchange systems to others that are trying to get the most out of existing equipment. Buying decisions, both in extension of useful life and with the purchase of new systems, is really driven by energy costs and total processing time. If a producer can get extended processing times without a capital purchase and minimal energy loss, then he will optimize the current equipment by either paying for an extended service or reconfigurations to maximize the energy usage. When all else is exhausted, the producers are purchasing new equipment.
Carlos Cobian, president, HRS Process Technology Inc.: They are looking for long running times. They do not want to stop a line to clean. The current status is a heat exchanger that can do a variety of products. Most companies now make numerous products that they cannot afford one heat exchanger for one application.
Don Bohner, manager, heat exchangers, Tetra Pak Inc.: Customers are looking for more reliable heat exchangers that can perform for longer hours with less energy costs and with low maintenance cost.
DFR: What special needs have arisen as processors seek to streamline operations and improve efficiencies?
Bohn: Dairy processors using plate-type heat exchangers are looking for designs that can save on utility costs without significant processing changes or installation costs. Processors also want to know they’re getting a proven, dependable product with design features that can improve the life span of the equipment. Also, dairy processors are concerned with plate designs that can maintain or improve CIP response.
LeClair: Much of the needs are really about equipment size. The requirement for processors to optimize their processing lines but keep them in the same manufacturing floor space, this means obtaining the best available technology at the lowest possible cost of ownership. This limits the approaches that can be used to help the plants become more streamlined. Serviceability is the other large hurdle for this initiative.
Cobian: Versatility.
Bohner: Energy costs have increased, new cultured and formulated products are being introduced, and operating capacities are being increased.
DFR: What new technologies have been developed to meet these needs?
Bohn: AGC has new frame designs that can “plug and play” with existing units, some over 30 years old. For example, some customers requiring new equipment, who are operating at 7,000 gph, can replace the only their existing plate pack (saving the frame capital expense) with a modern Pro5Plus (thicker 0.7 mm) plate and save over $30,000 in utility costs per year all with no piping changes. These same customers could also increase there production by over 20% (7,000 to 9,000 gph) due to the optimized Proflow plate design.
AGC has a new two-speed hydraulic frame that, in most cases, is the fastest opening/closing frames on the market. These hydraulic frames are compact and use simple, proven construction with no programming or tape measurements required. The frames even have the ability to automatically compensate for differences in total plates. The ability to replace an old, crumbling plate heat-exchanger frame with no piping changes means little downtime and big savings. Finally, some states or local power companies pay cash for energy saving retrofits or capital improvements.
LeClair: Plates like the NR5, which allows more plates to be installed within the same frame, offering up to 20% more surface area, which allows for better usage of the utilities, floor space and energy required.
Cobian: A SSHX that acts like a tubular heat exchanger and has the cleaning capability of a rational scrape – the best of both worlds.
Bohner: More efficient and larger heat exchangers have been introduced. An example is the Tetra Plex C15, with both a manual opening/closing and automatic opening/closing frame.
DFR: How are rising energy costs impacting development of these components?
Bohn: AGC is the leader in providing innovative designs and energy savings. Processors need to take advantage of every degree of heating or cooling energy available and be willing to pay the price now, as energy costs will only increase in the future.
LeClair: It is one of a few primary drivers of the designs of heat-exchange equipment. Much of the cost of operating a plant is based on the energy usage. This means every unit of energy that is saved goes directly to the bottom line.
Cobian: The less amount of operating costs the better. More companies are looking at connected horsepower more now than ever before.
Bohner: The manufacturers of heat exchangers are constantly improving the design of heat exchangers’ efficiency by improving the heat transfer surface area to be thinner but yet stronger; creating flow patterns to develop higher turbulence; and producing larger heat exchangers to process higher capacities at high efficiencies.
DFR: What’s the next phase of technological development on the way for heat exchangers?
Bohn: AGC heat transfer is constantly working to design faster, more compact frames with high quality, i.e. longer-lasting plates and gaskets.
LeClair: The next phase of development will really depend on a few items – first, the cost of energy. As the cost of energy rises, the more pressure processors will be under to improve their efficiencies, which in turn will drive the developments toward making the best use of that energy. Second, optimization of machine size; the ability of the manufacturers to be able to provide the same heat exchange capacity in a smaller footprint will be essential for the next phase of developments. This is driven by processors needing to produce more in the same plant space. Third, rethinking the materials used in producing heat exchangers driven by the cost of primary metals.
Cobian: A faster heater and cooler. Less time more throughput. The less time a product is exposed to the heating zone, the better the quality of your product.
Bohner: I see the next phase will be the development of equipment and software to maintain these heat exchangers. One of the more costly aspects in a processing plant is down time. Improved equipment and processes to maintain and monitor the key components of a heat exchanger will enable the processor to plan better for preventative maintenance and react more quickly for unplanned service, thus reducing down time.
Extras
AGC Heat Transfer Inc. www.AGCHeattransfer.com
APV www.apv.com
HRS Process Technology Inc. www.hrs-americas.com
Tetra Pak Inc. www.tetrapakprocessing.com